Wire EDM Service
Experience unparalleled precision and efficiency with our specialized Wire EDM services, delivering complex components in as fast as 2 days.
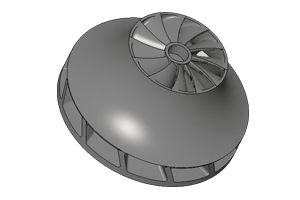
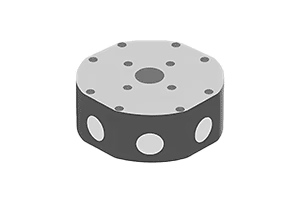
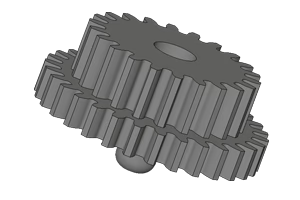
Start A New EDM Quote
STEP | STP | SLDPRT | IPT | PRT | SAT files
- All uploads are secure and confidential.
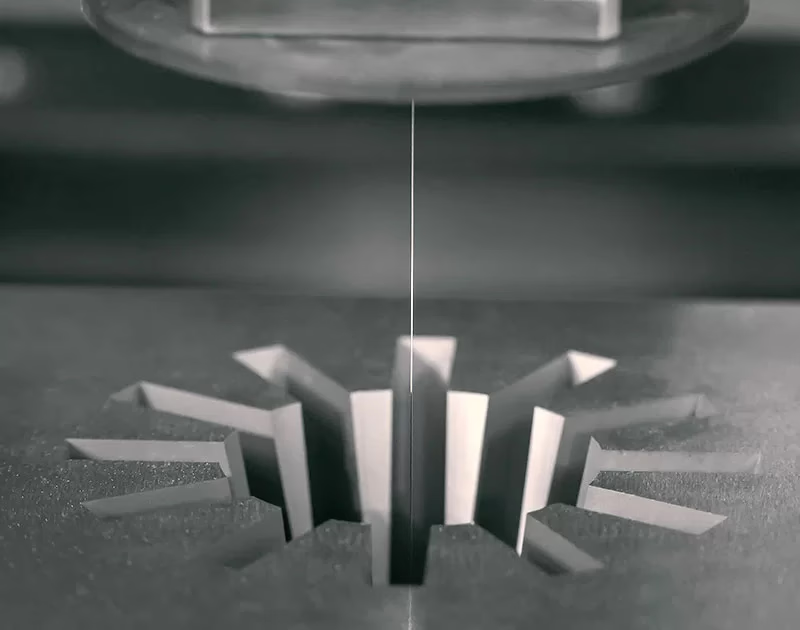
What does EDM stand for in machining?
Electrical Discharge Machining (EDM), also known as spark erosion, is a non-traditional manufacturing technique where material is removed from a workpiece through a series of repetitive electrical discharges or sparks. These sparks occur in a dielectric fluid between an electrode and the workpiece. This method excels at creating intricate shapes and detailed features in materials that are too hard or too delicate for traditional cutting tools. EDM is particularly valuable for producing molds, dies, and components with complex geometries where precision is paramount.
What is Electric Discharge Machining?
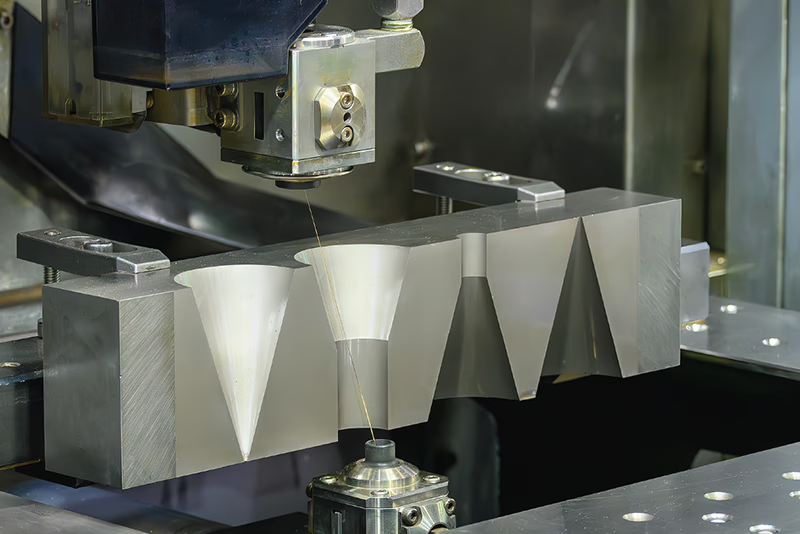
Our EDM Machining (Sinker EDM) Capabilities
Wire EDM | Sinker EDM | |
Tolerance level | ISO grade 7 to 12 | ISO grade 8 to 12 |
Part size | Min: 3.0×3.0x0.3mm | Min: 3.0×3.0x0.3mm |
Max: 300x300x200mm | Max:200x200x150mm | |
Materials | All metals | All metals |
Minimum fillet radius | 0.05mm standard | 0.05mm standard |
0.01mm premium precision | 0.01mm premium precision | |
Lead time | As fast as 3 days | As fast as 3 days |
EDM Machining (Sinker EDM) Materials
Sinker EDM, or die sinker EDM, is adept at working with all conductive metals and alloys, making it especially popular for machining hard materials such as steel alloys and carbide, while also being capable with softer, more malleable metals. We offer various material options for our sinker EDM projects, which cater to both the rigorous demands of hard material machining and the versatility needed for softer metals, ensuring suitability for a diverse range of applications.
Brass
Brass, also known as free-machining brass, is a highly adaptable material across various sectors. Its common uses span gears, lock parts, pipe fittings, and decorative items. With exceptional machinability, it can be effortlessly shaped and sized to meet specific requirements. Its attributes include superior corrosion resistance and good electrical conductivity, which make it particularly suitable for electrical components and marine environments.
Mill Lead Time:As fast as 3 days
Finishing Options:Media blasting
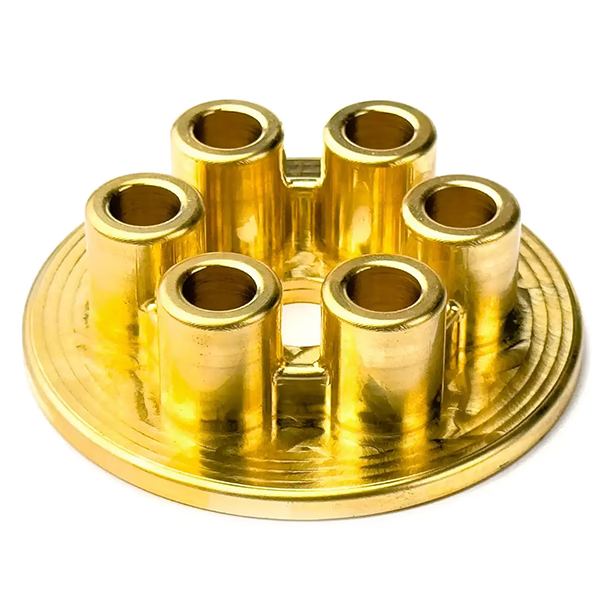
Copper
Copper grades 101 and 110 are known for their unparalleled thermal and electrical conductivity, making them ideal for applications such as bus bars, wire connectors, and various components in power transmission and distribution systems. These copper alloys also provide exceptional durability, resistance to corrosion, and are easy to fabricate.
Mill Lead Time:As fast as 3 days
Finishing Options:Available as-machined, media blasted, or hand-polished
Alloys:101, 110
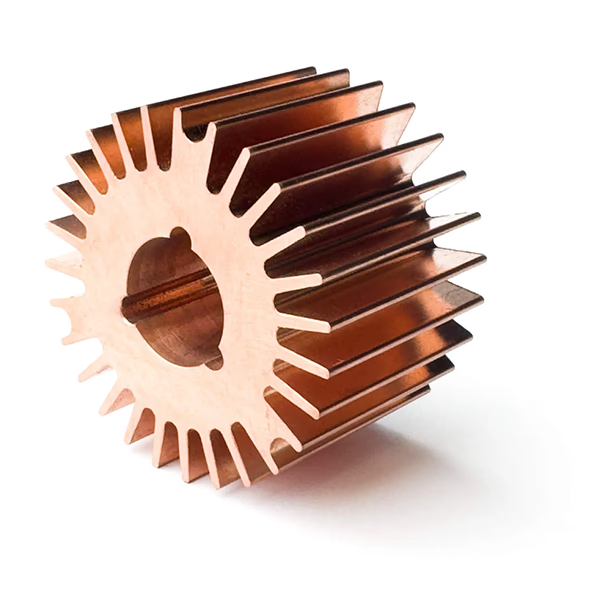
Aluminum
Aluminum is prized for being lightweight and incredibly versatile, finding extensive use across different sectors. Its key attributes include a superior strength-to-weight ratio, outstanding resistance to corrosion, malleability, and excellent thermal and electrical conductivity. These traits render aluminum perfect for applications requiring weight reduction, longevity, and effective heat dissipation, such as in engine blocks, heat exchangers, and various transportation parts.
Mill Lead Time:As fast as 3 days
Alloys:6061-T6, 7075-T6, 7050, 2024, 5052, 6063, MIC6
Finishing Options:Alodine, Anodizing Types II, III, III + PTFE, ENP, Media Blasting, Nickel Plating, Powder Coating, Tumble Polishing.
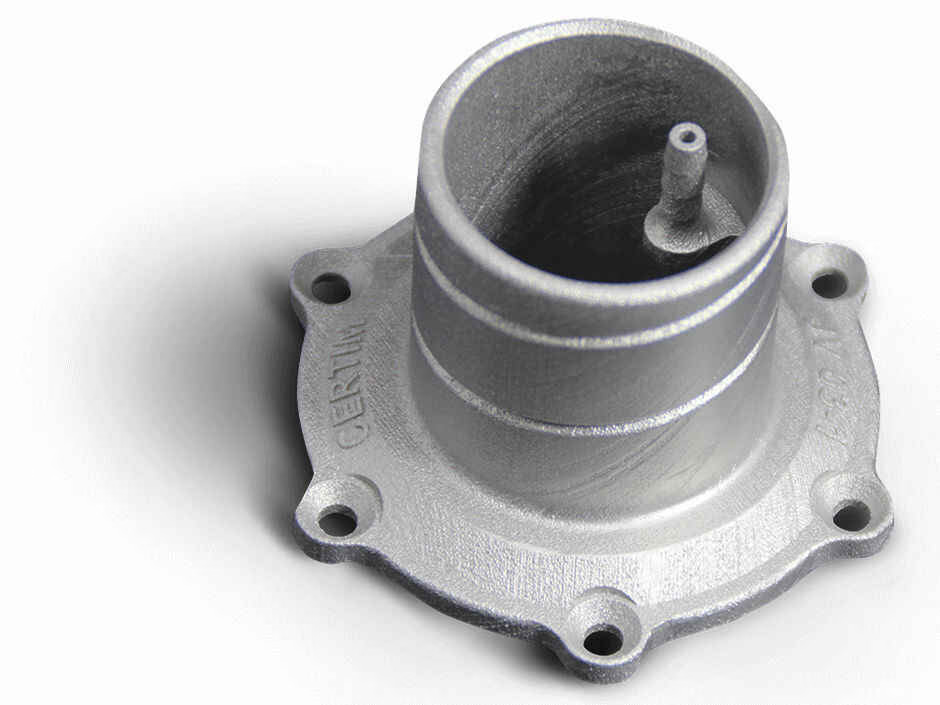
Titanium
Titanium stands out for its lightweight nature, strength, biocompatibility, and exceptional resistance to corrosion. With a remarkable strength-to-weight ratio and the ability to withstand high temperatures, it is extensively utilized in the aerospace and medical sectors. Applications include engine components, landing gear, structural parts, medical implants, and prosthetics. Additionally, titanium is employed in aerospace fasteners, turbine blades, sports gear, and marine equipment.
Mill Lead Time:As fast as 3 days
Finishing options:Media Blasting, Vibratory Tumbling, Passivation, Powdercoating
Grade:Titanium Grade 5
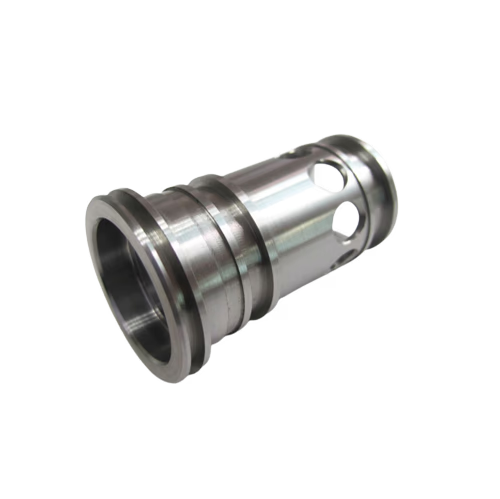
Stainless Steel
Stainless steel is celebrated for its versatility, boasting remarkable strength, durability, and resistance to both high temperatures and corrosion. Its applications span multiple industries including construction, automotive, aerospace, and manufacturing. Common uses include heat exchangers, industrial ovens, exhaust systems, construction machinery, heavy equipment, engine parts, fasteners, turbine blades, tanks, pumps, valves, as well as orthopedic implants and medical devices.
Mill Lead Time:As fast as 3 days
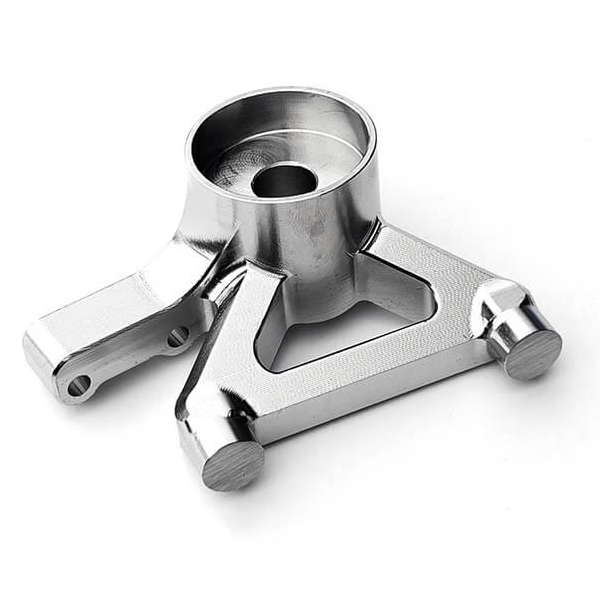
Steel
We offer an extensive selection of steel varieties to cater to diverse application needs. Alloy and carbon steel are especially effective for manufacturing fixtures, mounting plates, draft shafts, axles, torsion bars, gears, bolts, studs, shafts, and structural elements. These high-quality steel options deliver superior strength and durability, perfect for rigorous industrial uses.
Mill Lead Time:As fast as 3 days
Alloys:4140, 4130, A514, 4340
Carbon Steel Types:1018 Low Carbon, 1045 Carbon, Galvanized Low-Carbon
Finishing Options:Black Oxide, ENP, Electropolishing, Media Blasting, Nickel Plating, Powder Coating, Tumble Polishing, Zinc Plating, Vibratory Tumbling
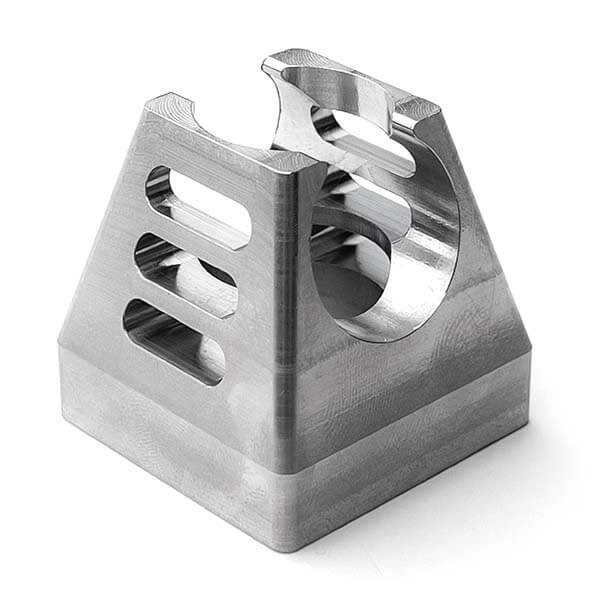
EDM Machining – Applications
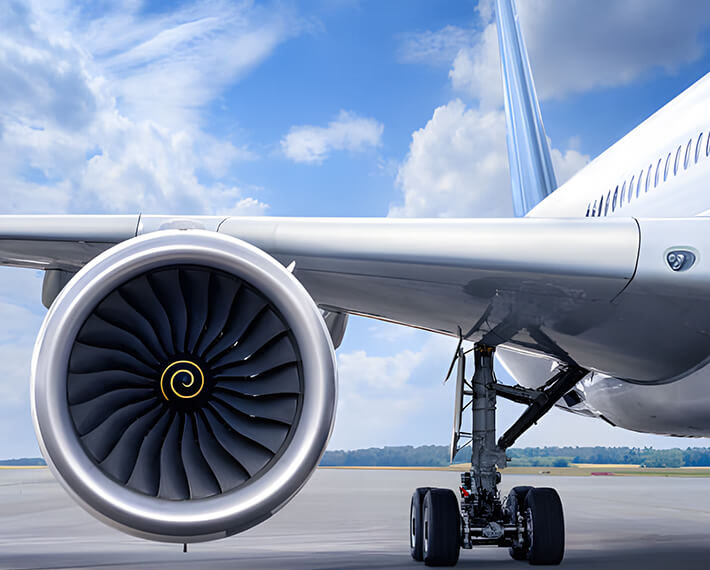
Aerospace
Precision manufacturing boosts aerospace development.
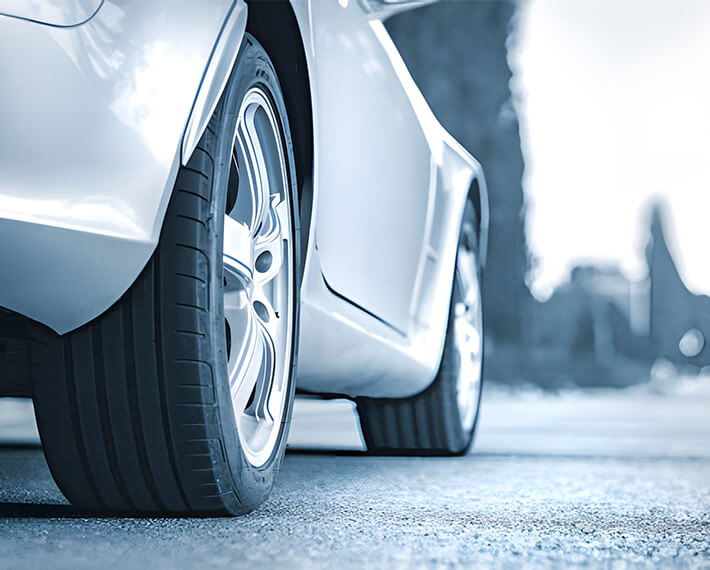
Automotive
Automotive grade certified precision parts.
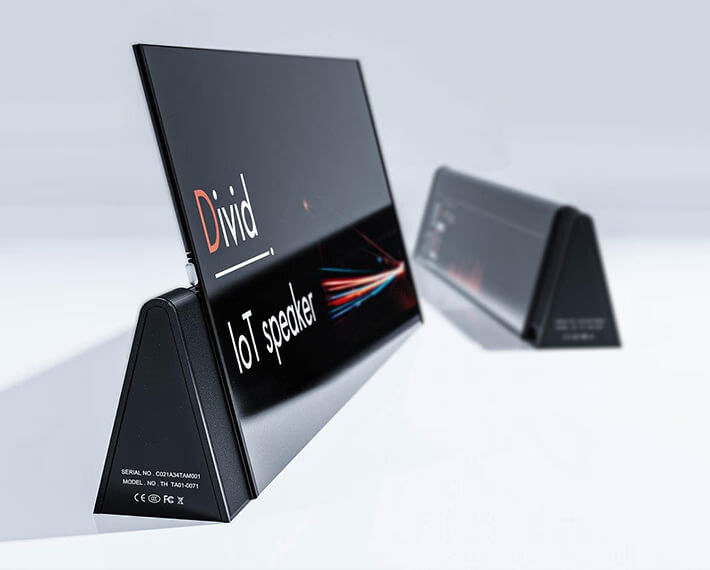
Consumer Products
First choice for new product launches
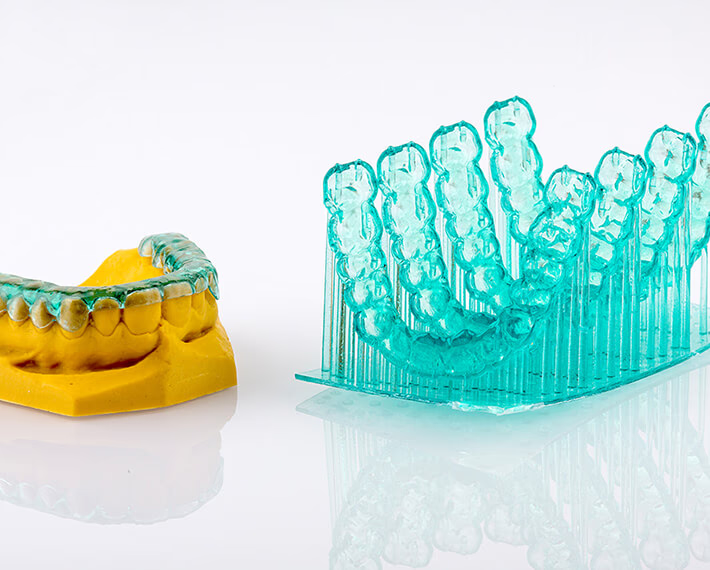
Medical
Medical grade certified precision parts
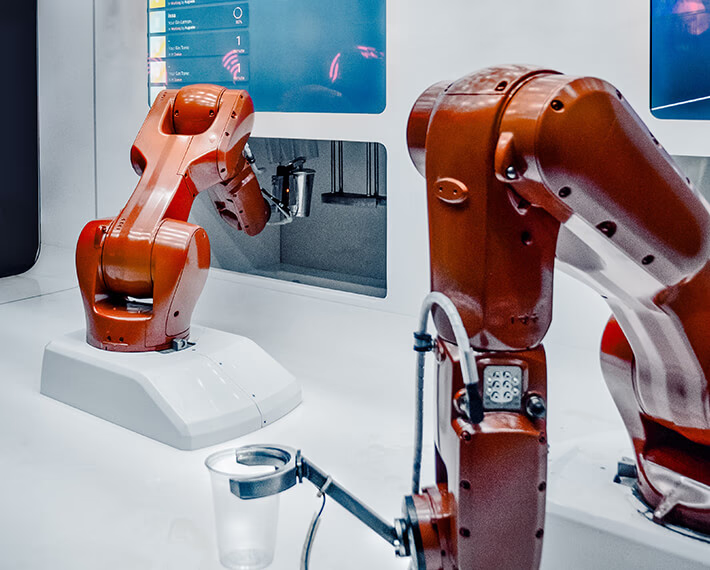
Robotics
Accelerate the development of the future robotics industny
Advantages of Die Sinking EDM
Die Sinker EDM excels at achieving tight tolerances and superior surface finishes on blind features that are challenging with conventional machining methods. The advantages of employing Die Sinker EDM are numerous:
- Precision and Accuracy: It ensures high precision, even on complex internal geometries.
- Surface Quality: Produces excellent surface finishes, often eliminating the need for further polishing.
- Complex Shapes: Capable of creating intricate shapes, including undercuts and deep cavities.
- Hard Material Compatibility: Efficiently machines materials that are too hard for traditional tools.
- No Mechanical Stress: The non-contact nature protects delicate parts from distortion.
- Consistency: Offers high repeatability for identical parts production.
- Reduced Post-Processing: Minimizes burr formation, reducing the need for additional finishing work.
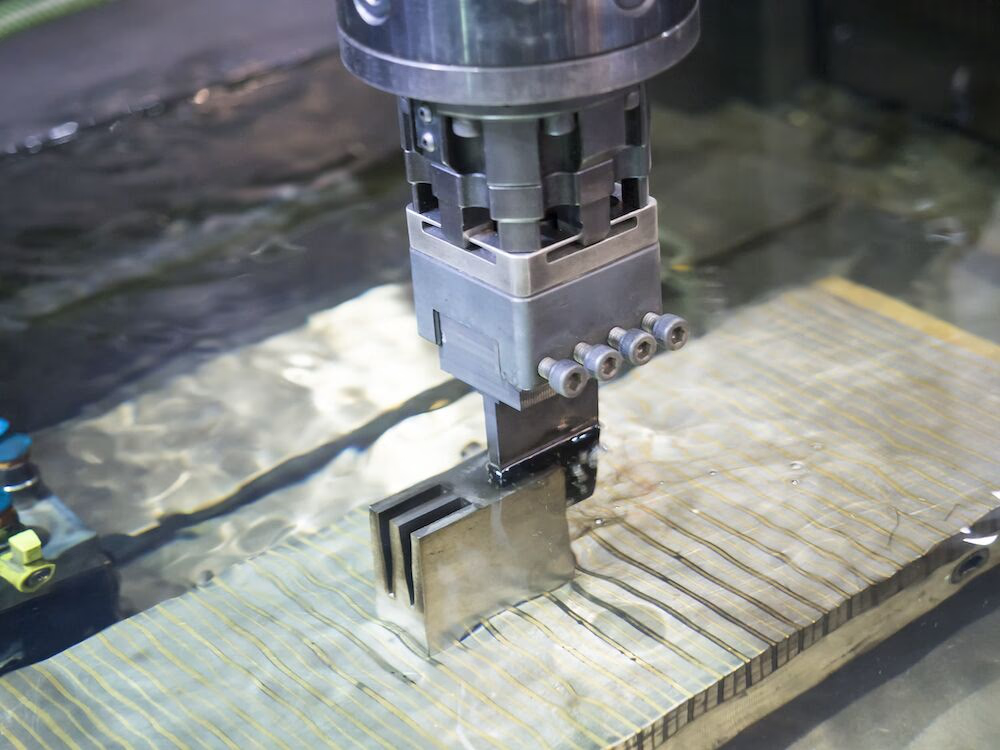
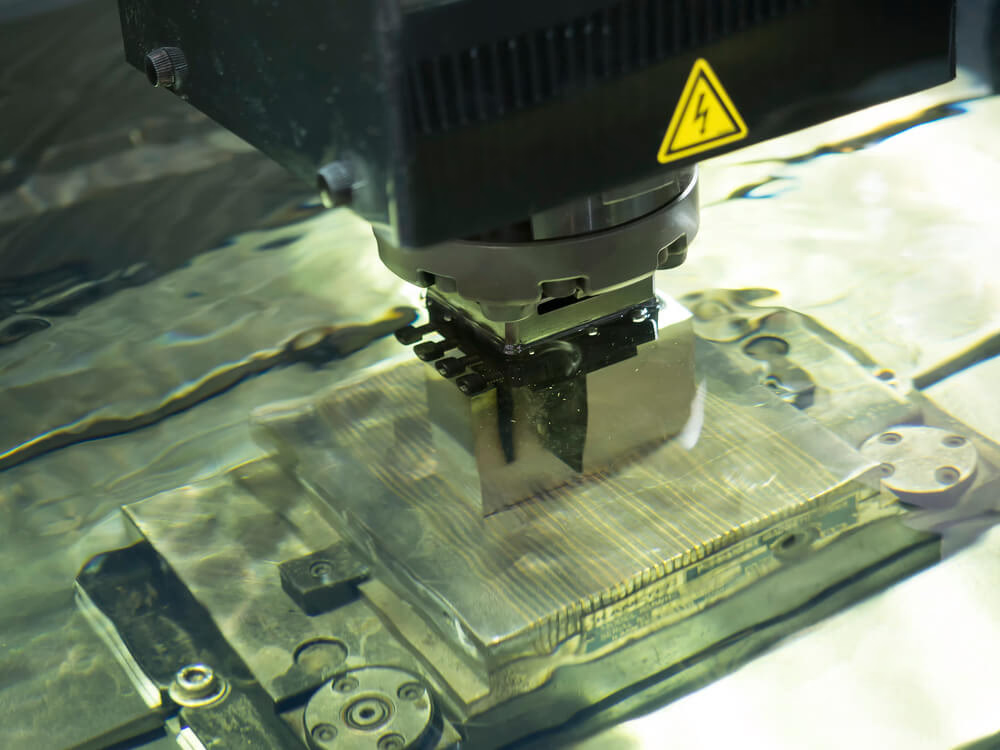
Limitations of Die Sinking EDM
Die sinking EDM (Electrical Discharge Machining) offers numerous advantages and a broad spectrum of capabilities, but it also comes with certain limitations that must be considered when selecting a manufacturing method for parts.
- Material selection is limited to conductive materials
- Slow material removal rate when compared to other machining processes
- Electrodes can be expensive and they wear
- High cost associated with complex machines
- Due to the high heat generated by the sparks, there can be a small heat affected zone and recast layer left on the machined surface
- Secondary processing may be required to remove the recast layer
Advantages of Wire EDM
Wire EDM (Electrical Discharge Machining) indeed provides several unique advantages over traditional CNC milling. Here are some of them with a bit of polish:
- Precision and Accuracy: Wire EDM can achieve extremely tight tolerances, often down to ±0.005 mm, which is crucial for industries like aerospace and medical device manufacturing where precision is paramount.
- Complex Geometries: Unlike milling, which can be limited by tool access, Wire EDM can cut intricate shapes with internal corners and features that would be difficult or impossible to machine with conventional tools. This is because the wire electrode can navigate through very narrow and complex paths.
- No Mechanical Stress: Since Wire EDM removes material by thermal erosion rather than mechanical cutting, there's virtually no physical stress on the workpiece. This makes it ideal for materials that are sensitive to stress, like hardened tool steels.
- Hard Material Handling: Wire EDM excels at cutting through hard materials such as titanium, carbide, and hardened steel without the need for special tooling or additional heat treatment to soften the material before cutting.
- No Burr Formation: The process generally results in burr-free cuts, reducing or eliminating the need for secondary deburring operations, which saves time and costs.
- Taper Cutting: Wire EDM can cut parts with angled or tapered walls, allowing for the production of dovetail grooves or angled features in one setup, which would be challenging with milling.
- Automated and Consistent: Once set up, Wire EDM can run for long periods with minimal human intervention, leading to high repeatability and consistent quality in production runs.
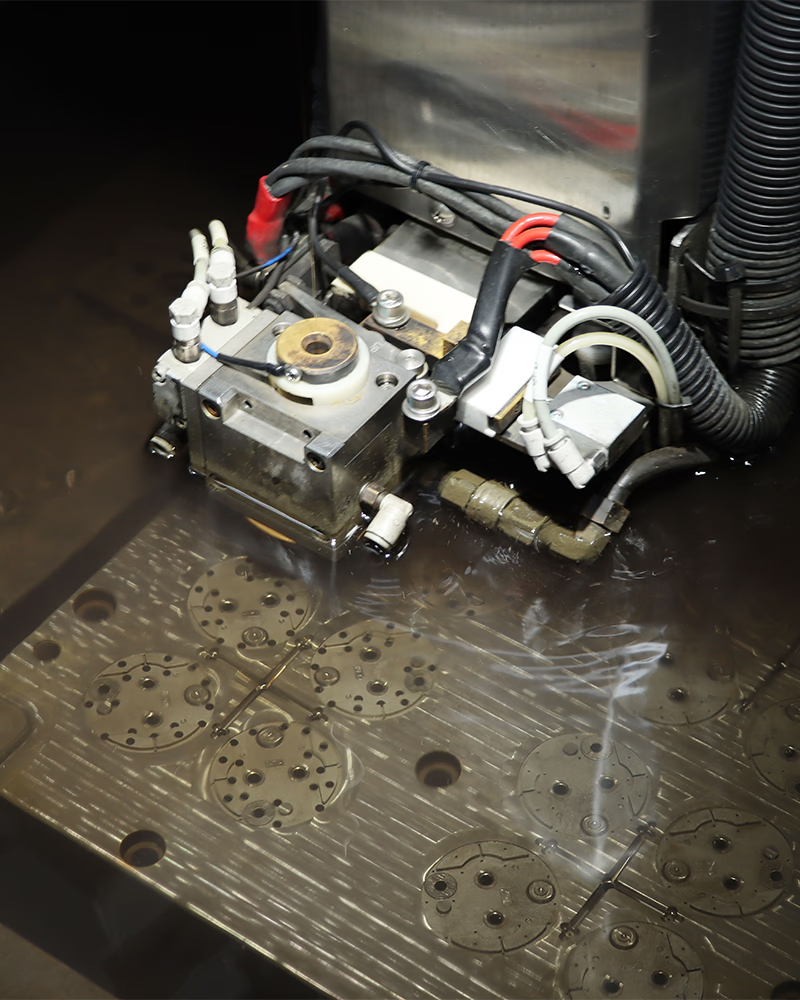
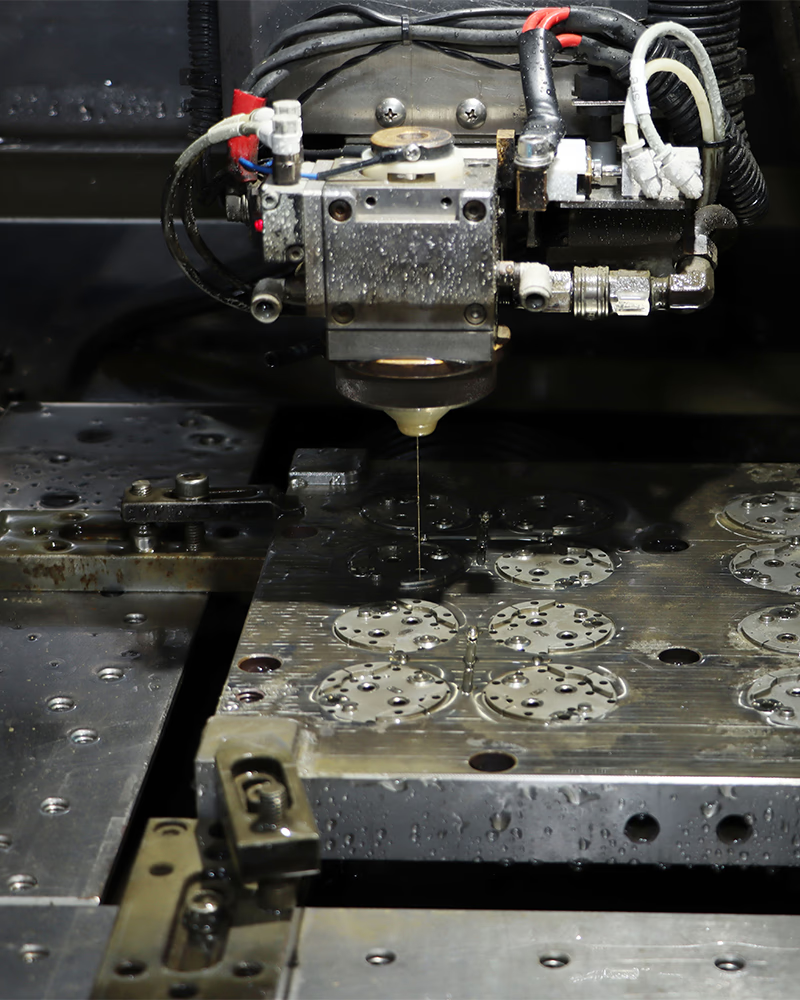
Limitations of Wire EDM
While Wire EDM offers significant advantages in manufacturing complex geometries, there are indeed several limitations to consider:
- Conductive Materials Only: Can't machine non-conductive materials like ceramics or plastics.
- Slow Cutting: Slower for large or thick parts, increasing time and cost.
- Surface Recast: Cuts may have a recast layer needing post-processing for critical surfaces.
- Kerf Loss: Material loss due to wire width limits fine feature size.
- Heat-Affected Zone: Risk of altering material properties near the cut.
- High Setup Costs: Expensive initial setup for small batches or complex parts.
- Depth Limitations: Constrained by wire length and stability.
- Environmental Impact: Generates wire waste and involves managing dielectric fluid.
EDM Machining Services in Manufacturing
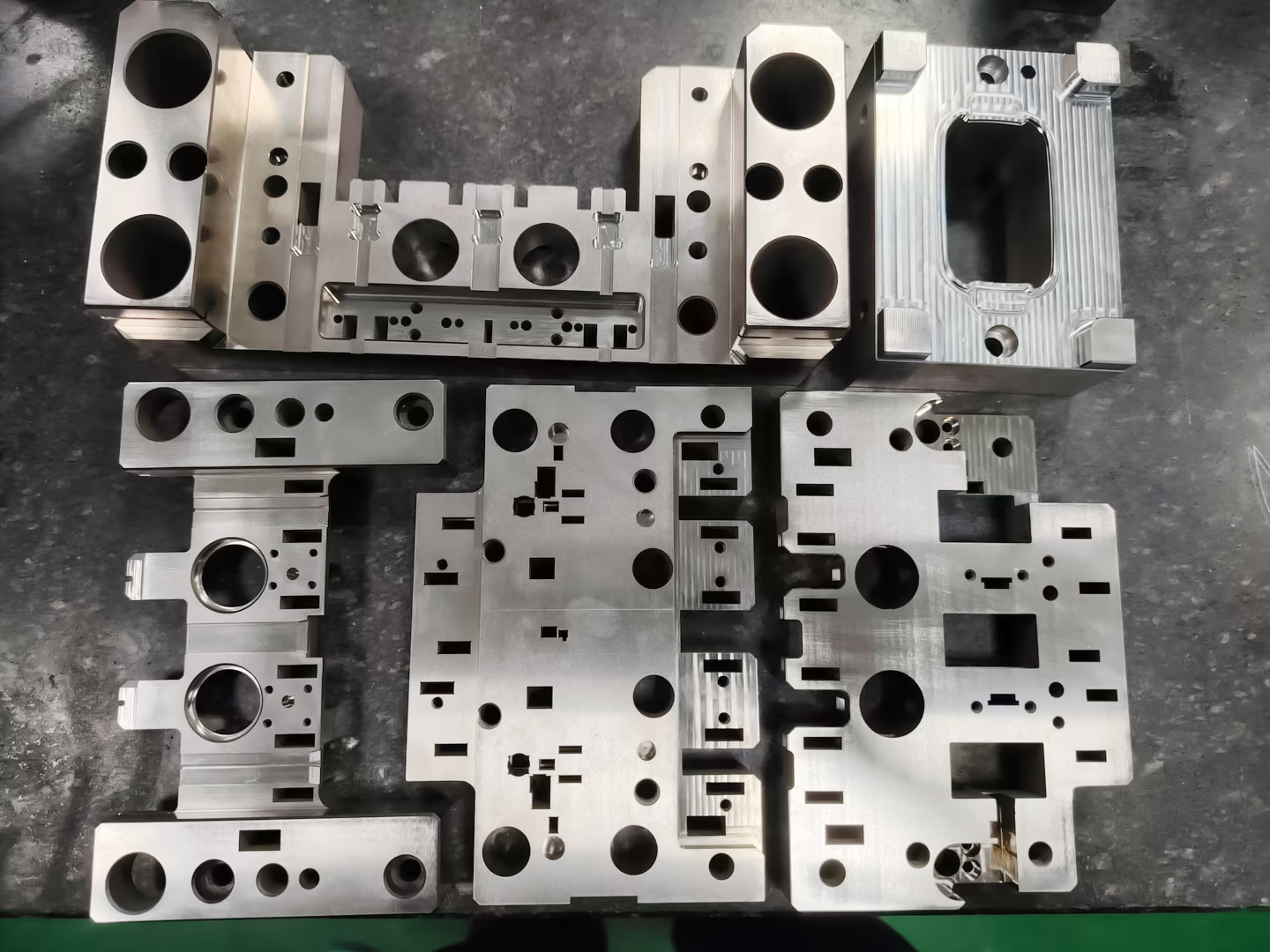
Let’s Build Something Great, Together