Precision Grinding Services
High-quality Precision Grinding Services in Days Not Weeks
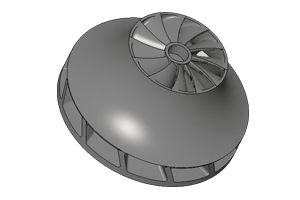
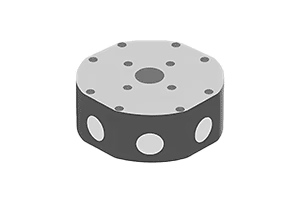
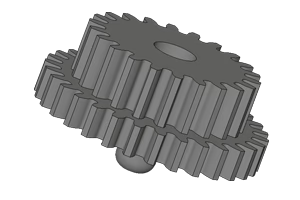
Start A New Precision Grinding Quote
STEP | STP | SLDPRT | IPT | PRT | SAT files
- All uploads are secure and confidential.
What Is Precision Grinding?
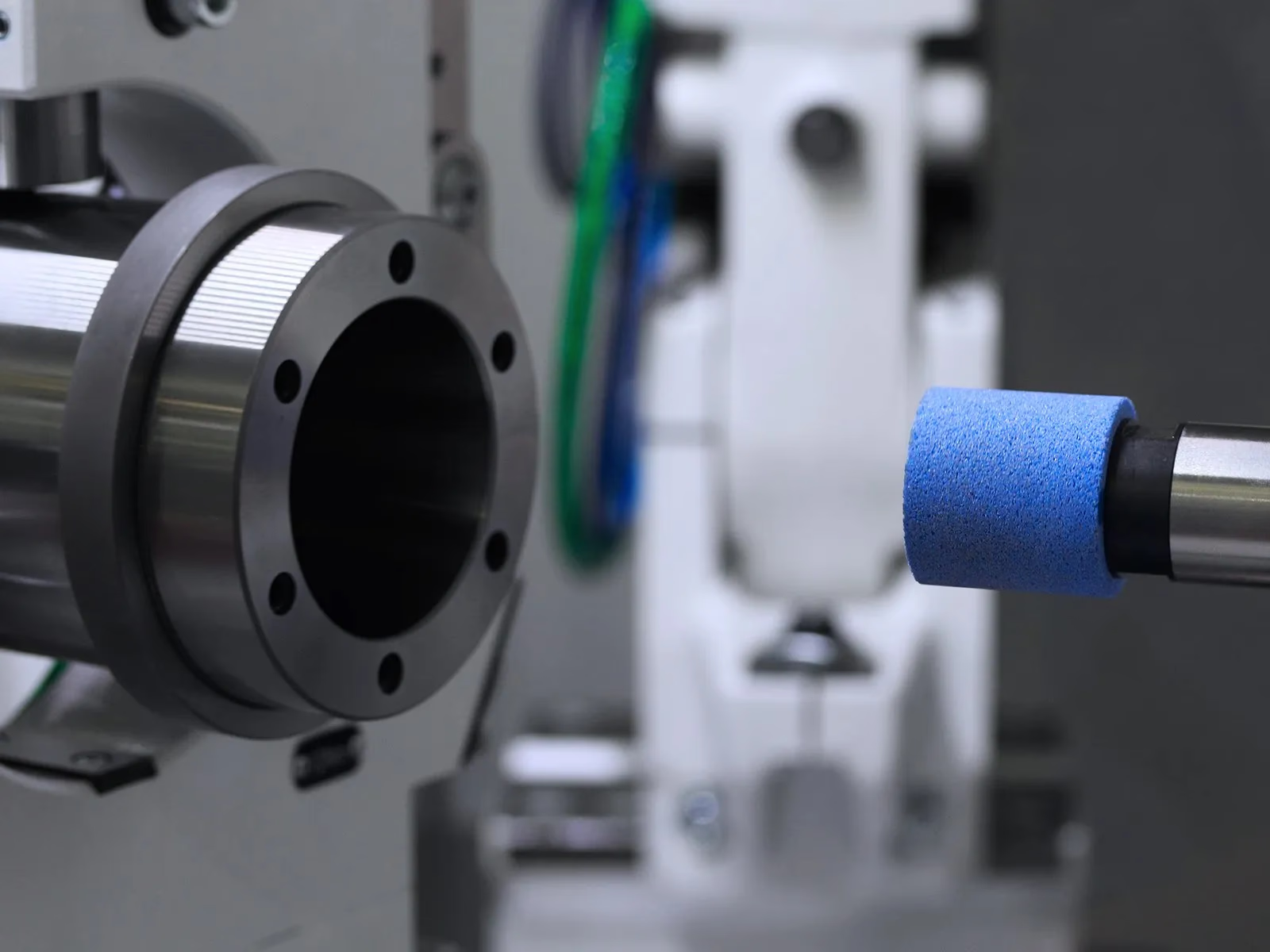
Precision grinding is a finishing process used in manufacturing to remove small amounts of material from a workpiece. An abrasive grinding tool, usually a rotating wheel or belt, contacts the workpiece and facilitates material removal. Grinding is typically used as a finishing process and is a cost-effective and reliable way to obtain precise tolerances and beautiful surface finishes on a manufactured part. Precision grinding is often used to satisfy highly precise tolerances as low as +0.00025”. Additionally, the process is often used to obtain polished surface finishes on parts. Precision grinding can be used as a final finishing process or can be used to prepare parts for other finishing processes like honing, lapping, and superfinishing.
Precise dimensions and desirable surface finishes are made possible in precision grinding processes by the use of abrasives such as: aluminum oxide, silicon carbide, and diamond. The type of abrasive used depends on the workpiece material. For example, aluminum oxide abrasives are best for grinding steel and other ferrous metals, while silicon carbide abrasives are better for non-ferrous metals. While grinding can be completed manually using equipment like belt grinders and angle grinders, CNC automated grinding produces superior results in terms of efficiency and surface quality.
Types of Precision Grinding
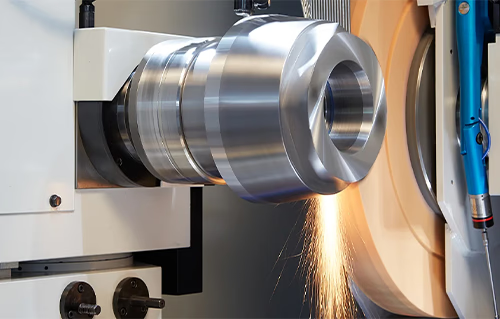
Cylindrical Grinding
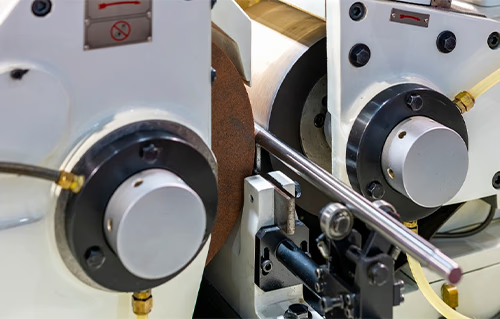
Centerless Grinding
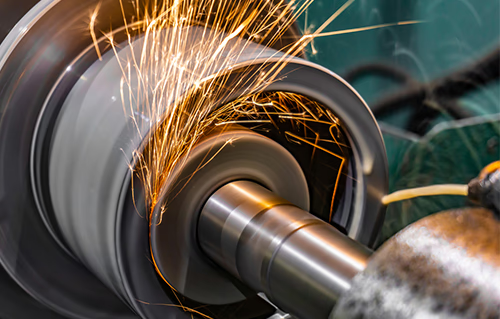
Internal Grinding
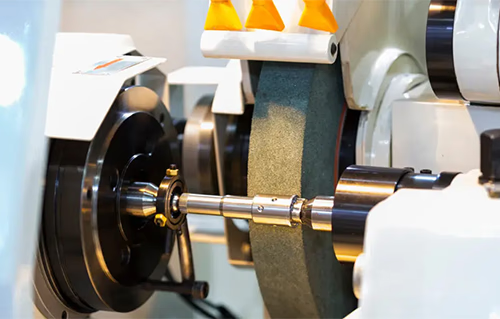
Spindle Grinding
Benefits of Precision Grinding
1. Cost-Effectiveness
Precision grinding is a cost-effective process because of its ability to achieve precise dimensions in large volumes of parts. Not only is the process fast, but it’s also versatile and highly reliable. Precision grinding can be used on a wide array of materials, including hardened steel and non-ferrous metals, and seldom produces non-conforming parts.
2. Accuracy
A high degree of accuracy is a huge advantage of precision grinding. In manufacturing, machining processes like milling and turning are used to achieve dimensions close to what is required. While required dimensions can often be achieved with these machining processes, grinding enables manufacturers to remove tiny amounts of material to create extremely accurate parts.
3. Reliable
Precision grinding is a highly reliable process. Defects seldom occur during grinding processes, since the process is easy to set up, highly efficient, and applies less pressure to the workpiece than other processes used to obtain precise dimensions like machining.
4. Tight Tolerances
Tight tolerances are another advantage of precision grinding. With precision grinding, Xometry can achieve tolerances as tight as +0.00025”. Tolerances this low are great for parts commonly manufactured for the automotive, aerospace, and medical industries. Especially in the medical industry where parts are fitted to or implanted into a person’s body, precise parts are absolutely essential.
5. Smooth Surface Finishes
Precision grinding produces very smooth surface finishes. This is important not just for functionality, such as in medical parts like surgical instruments, but also for the aesthetic qualities of the finished product.
Drawbacks of Precision Grinding
1. Time-Consuming
Precision grinding takes time, which makes it expensive. Fabricators and customers should agree on whether this process is really necessary, or whether the tolerances achieved by milling or turning will be sufficient for the application.
2. High Initial Investment
Precision grinding machines require a high initial investment. Making the business case for this type of capital expenditure requires a close study of the current business cash flow and the projections for increased business due to the increased process capability offered by having a precision grinding machine in-house.
3. Could Contaminate Parts
For parts that require high purity such as in the medical, semiconductor, and food service industries, precision grinding could leave behind debris from either the grinding wheel abrasive or the small particles removed from the part surface. Such contaminants can compromise the function or cleanliness of the part.
In need of custom precis
Let’s Build Something Great, Together