Metal 3D Printing Service
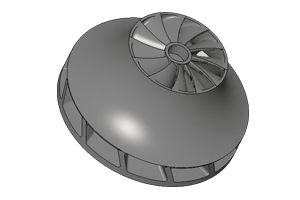
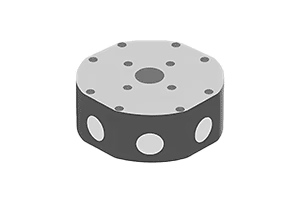
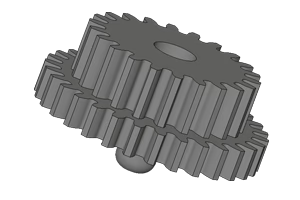
Start A New DMLS Quote
STEP | STP | SLDPRT | IPT | PRT | SAT files
- All uploads are secure and confidential.
How a Direct Metal Laser Sintering Machine Works?
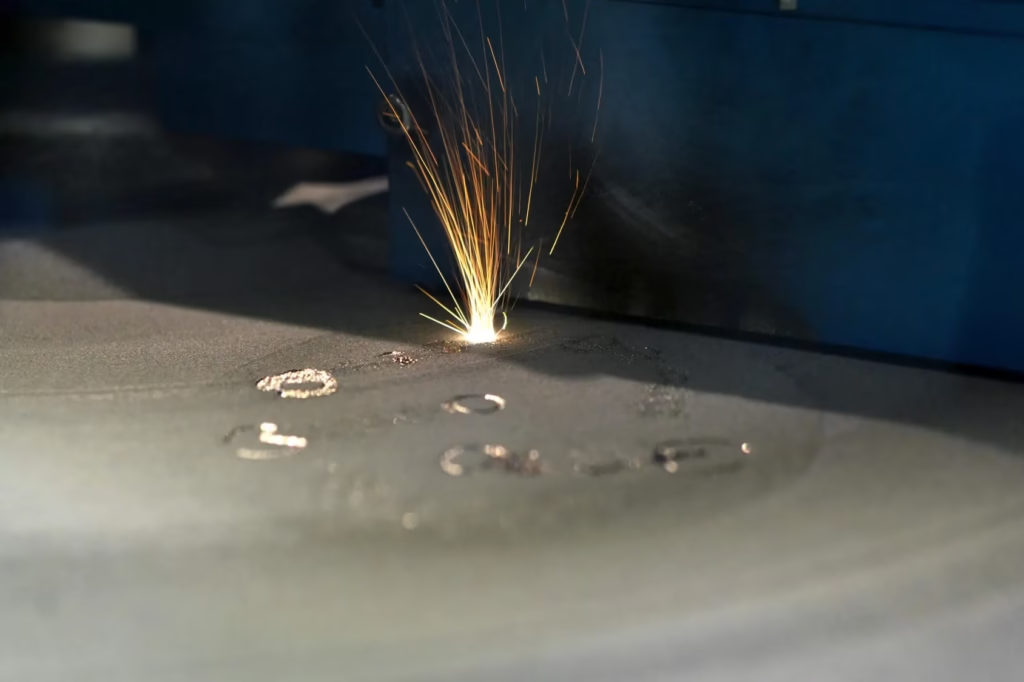
Direct metal laser sintering (DMLS) is an additive metal printing technology that builds metal parts from a CAD file by selectively fusing stainless steel or aluminum powder into thin layers.
Direct metal laser sintering’s layer-by-layer printing allows multiple parts to be combined during the printing process. With traditional manufacturing processes, metal parts are machined or metal casted into several parts and assembled. Printing an all-in-one assembly strengthens the finished part while reducing the weight and cost of production significantly. DMLS techniques can also create parts at a high density. This is ideal for parts under high pressure such as in oil and gas industries.
Direct Metal Laser Sintering 3D Printing Capabilities
Feature | Description |
---|---|
Build Size |
10″ x 10″ x 10″ (250 x 250 x 250 mm) |
General Tolerances |
+/- 0.005” for the first inch is typical, plus +/- 0.002” for every inch thereafter |
Layer Height |
.0012” – .0016″ depending on material |
Surface Roughness |
150-400 µin Ra, depending on build orientation and material used for the build |
Infill |
100% |
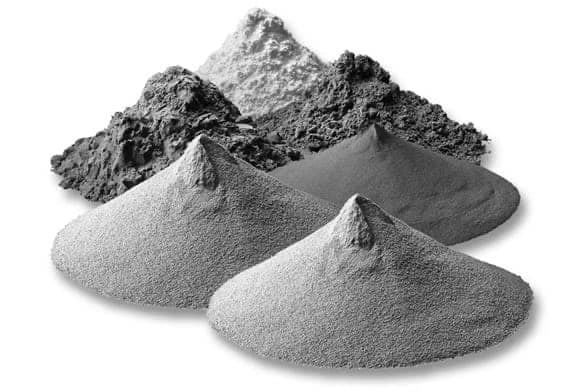
Metal 3D Printing Material
Stainless Steel 17-4 PH is a precipitation hardened stainless steel that is known for its hardness and corrosion resistance. If needing a stainless steel option, select 17-4 PH for its significantly higher tensile strength and yield strength, but recognize that it has far less elongation at break than 316L. Final parts built 17-4 PH receive vacuum solution heat treatment as well as H900 aging.
Primary Benefits
- Heat treated for full hardness and strength
- Corrosion resistance
Choose 316L when stainless steel flexibility is needed; 316L is a more malleable material compared to 17-4 PH. Final parts built in 316L receive stress relief application.
Primary Benefits
- Heat treated for full hardness and strength
- Corrosion resistance
Aluminum (AlSi10Mg) is comparable to a 3000 series alloy that is used in casting and die casting processes. It has good strength -to-weight ratio, high temperature and corrosion resistance, and good fatigue, creep and rupture strength. AlSi10Mg also exhibits thermal and electrical conductivity properties. Final parts built in AlSi10Mg receive stress relief application.
Primary Benefits
- High stiffness and strength relative to weight
- Thermal and electrical conductivity
Inconel is a high strength, corrosion resistant nickel chromium superalloy ideal for parts that will experience extreme temperatures and mechanical loading. Final parts built in Inconel 718 receive stress relief application. Solution and aging per AMS 5663 is also available to increase tensile strength and hardness.
Primary Benefits
- Oxidation and corrosion resistance
- High performance tensile, fatigue, creep, and rupture strength
Cobalt Chrome (Co28Cr6Mo) is a superalloy comprised primarily of cobalt and chromium. It's high tensile strength and resistance to creep and corrosion makes it a good material choice for aerospace components and medical instrumentation.
Primary Benefits
- High performance tensile and creep
- Corrosion resistance
Titanium (Ti6Al4V) is a workhorse alloy. When measured against Ti grade 23 annealed, the mechanical properties of Ti6Al4V are comparable to wrought titanium for tensile strength, elongation, and hardness.
Primary Benefits
- High stiffness and strength relative to weight
- High temperature and corrosion resistance
These figures are approximate and dependent on a number of factors, including but not limited to, machine and process parameters. The information provided is therefore not binding and not deemed to be certified. When performance is critical, also consider independent lab testing of additive materials or final parts.
Available Finishes
- Standard: In addition to the removal of support structures, the part surface is media blasted to provide a uniform finish.
- Custom: Additional DMLS post-processing, such as CNC Machining of features and polishing, are evaluated on a case-by-case basis and can be requested in the quoting tool.
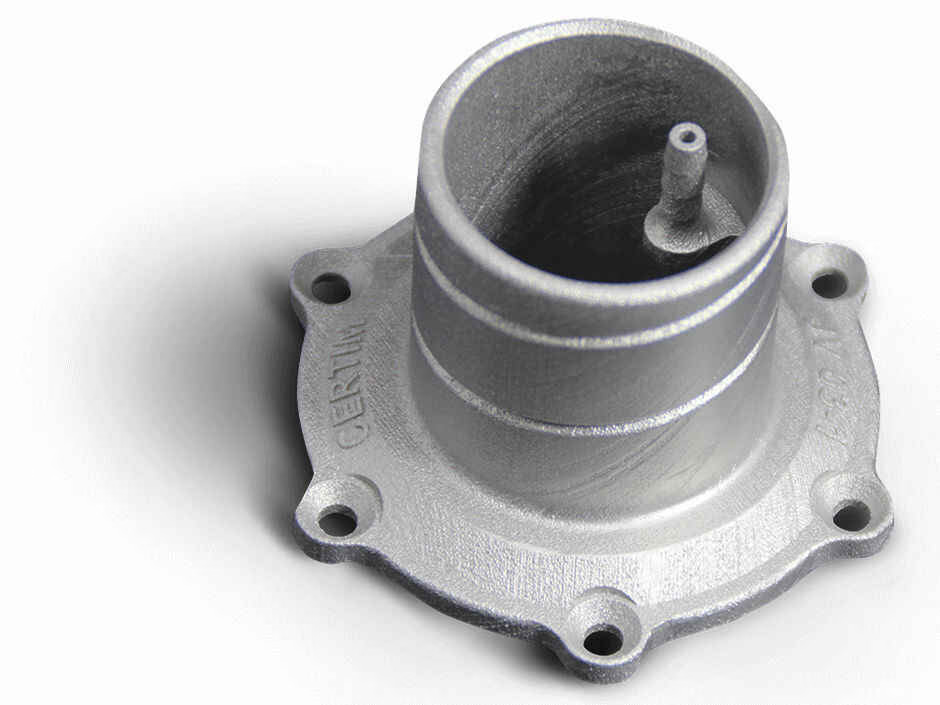
Best Applications for DMLS
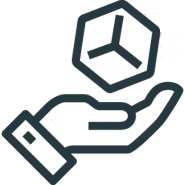
Rapid Tooling
Because DMLS parts are strong yet lightweight, they are widely used for rapid tooling, fixtures, and jigs.
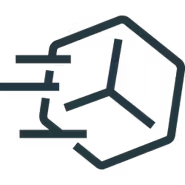
Rapid Prototyping
DMLS metal laser printing is typically affordable and fast, and therefore is often used to make proof-of-concept models and fully functional late-stage prototypes.
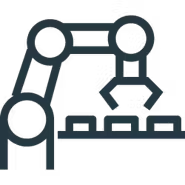
Production
Cast-quality finish (fully dense) and durable materials make DMLS printing a favorite technology for end-use products.
Let’s Build Something Great, Together